We are manufacturer, Exporter and Supplier of Encapsulating Type Leak Clamp are an essential part of our suite of pipeline integrity products. Available in a wide variety of sizes, ratings and arrangements, the clamp product line can be supplied independently or as an add-on to larger repair systems.
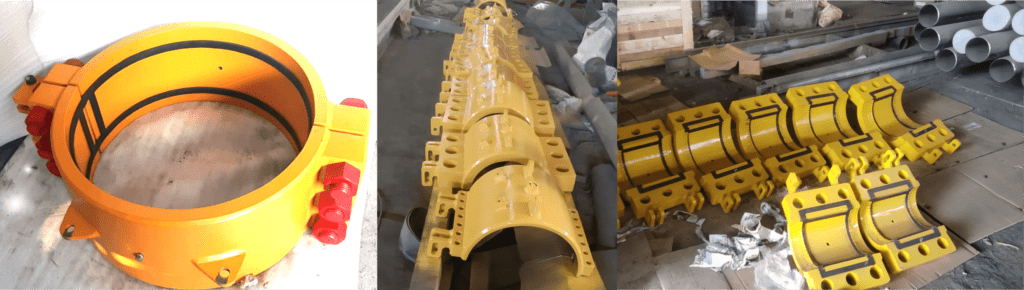
What is Encapsulating Type Leak Clamp ?
The sealing arrangement provides full containment around the damaged section of pipe (leak sealing only). If required, we can design the clamp to have a gripping section to provide a fully permanent structural repair that can be DNV-GL Product Certified.
Suitable for onshore, topside, diver installed or deepwater remote repair, our engineered MORGRIP clamps provide an increased lev-el of safety and reassurance when repairing critical pipelines or being stored as part of an emergency pipeline repair system or contingency plan.
Our clamps are application specific and designed, forged and fabricated to the exact requirements of the operator and repair location. This bespoke service ensures a fully configurable solution of the highest quality.
Special Specification for Dome Shaped Encapsulating type Leak Clamp:
- The functon of Dome type Encapsulaaon Leak Repair Clamp is to encapsulate any, branch Leaking / Non reliable fi ng on
- The Clamp consists of Two Halves with one half having a Branch
- The Clamp is pressurized unequally due to Dome on one The same needs to be considered during design.
- The Clamp shall be provided with all associated Valves and fii ng for successful and convenient installati Vent Valves, Pressure Gauge and liGin belts are to be provided as a minimum.
- The Clamp shall be suitable for welding to mainline at a convenient time aaGer installatio .
- One Spare set of seal shall be provided in Nitrogen Purged Aluminium
General Technical Specifications for Encapsulating type Leak Clamp
Dome SHAPED encapSULAtng type leak clamp a SSembled with StudS, NUTS and BESt quality SEALIng material whole body aS per the SPECIfiCCati memeoned below:
S. No. |
Description | Parameters |
1 | Design | As per API6H/ ASME SEC VIII DIV.1 / ASME SEC VIII DIV.2 |
2 | Service/ Product to be handled | Petroleum Product |
3 | Suitable for fixing on Spiral / Longitudinal weld pipe of grade |
4 |
Body | i. Carbon steel plates of weld-able quality (Carbon maximum – 0.25%), ii. Shell – ASTM A 516 Gr. 70, iii. Stiffener – ASTM A105. iv. Longitudinal length of leak clamp should be minimum |
5 |
Studs | i. Alloy steel weld able conforming to ASTM A193- B7 / EN- 19 (minimum 7 nos. studs on either side). Preferable size stud (Diameter) should be 7/8”. ii. Studs length 4 nos. (Two on each side) should be 12 inch length and balance 9 inch length. iii. All stud / bolts supplied shall be hot dipped galvanized as per ASTM A 153 |
6 |
Nuts | i. Alloy steel weld able quality confirming to ii. ASTM A194 Gr. 2H/ EN- 8 iii. Spot facing of the nut seal shall be carried out and no washer shall be used for tightening the nuts. iv. All nuts shall be hot dipped galvanized as per ASTM A 153 |
7 |
Sealing Material | i. There shall be sealing ring groove of appropriate size on the inner side of the leak clamp body on periphery of clamp. The mol ded rubber shall cover the groove and covered surface between groove. ii. Best quality “Buna N” rubber packing material iii. Approximately 6 mm thick shall be used. The minimum thickness of packing material on surface of body & outside of groove may be 3 – 4 mm. iv. Shelf life of complete material should be minimum 4 year (confirmation is required from bidder in writing) v. The Seal Material of Clamp shall be suitable for hydrocarbon with following specifications:- · MATERIAL :BUNA N · SHORE HARDNESS: 80 +/- 5 A · TENSILE STRENGTH: 150 KG/CM2 MINIMUM · ELONGATION AT BREAK: 150% MINIMUM. · COMPRESSION SET: 15% MAX. |
8 |
Edge Preparation | i. Edge as per ASME B -31.4 shall be done to be welded including nuts & studs of leak clamp. ii. The circumferental ends shall be chamfered (approx 45 deg.) down to thickness of the pipe (i.e. 0.281”) as per ASME B 31.4, secti n 451.6.2 I 6. |
9 |
Hydro test Pressure | 29.0 kg/cm2 for Class 150 at ambient temperature. 152.0 kg/cm2 for Class 600 at ambient Temperature. 228.0 kg/cm2 for Class 900 at ambient Temperature. The seals shall be replaced upon completion of hydro test. Testing shall be carried out in presence of Owner’s representative. No visual bulge shall be accepted during hydro test. |
10 |
Finishing | Two coats of Zinc Silicate primer with minimum Coati g thickness of 100 micron uniformly applied on body (uncovered by seal) of the leak clamp. |
11 |
Others | Clamps to be painted with airless spray gun. Primer: Zinc Silicate – 75DFT, Intermediate Coat – MIO 50DFT, T op Coat – Epoxy Polyurethane – 40DFT |
Compliance to Specification:
- The bidder should comply with the specificaton in totality and in token of confirmmaon the bidder shall return a copy of specification duly signed &
- Any remark by the bidder in respect of specificaaon shall be mentone d herein below with proper reference to the clause and appropriate reason for the
- Any remark directly or indi rectly on the spec ificaton by the bi dder made else where in the offer shall not be considered by the
Table 1. Imensions Details for High Pressure Long Seal Leak Clamps
Note: * Tolerance ± 3mm
BILL OF MATERIAL | |||
Sr. No. | DESCRIPTION | MATERIAL | REMARKS |
01 | SPLIT BODY SHELL | ASTM A 516 GR 70 |
|
02 | STIFFNERS | ASTM A 105 |
|
03 | STUDS | ASTM A193 GR B7 |
|
04 | NUTS | ASTM A 194 GR 2H |
|
05 | SEALING GASKET | BUNA ‘N’ |
|
06 | LIFTING HOOK | ASTM A 516-70 |
|
07 | BRANCH PIPE | ASTM A 106 Gr B |
|
08 | CAP | ASTM A 234 GR. WPB |
|
Note: Following requirements to be fulfilled by the parres:-
- Approval for QAP and man ufacturing procedure, draw ing of leak clamp, design of e ach clamp, Material test certificates before start of producton / man
Drawings
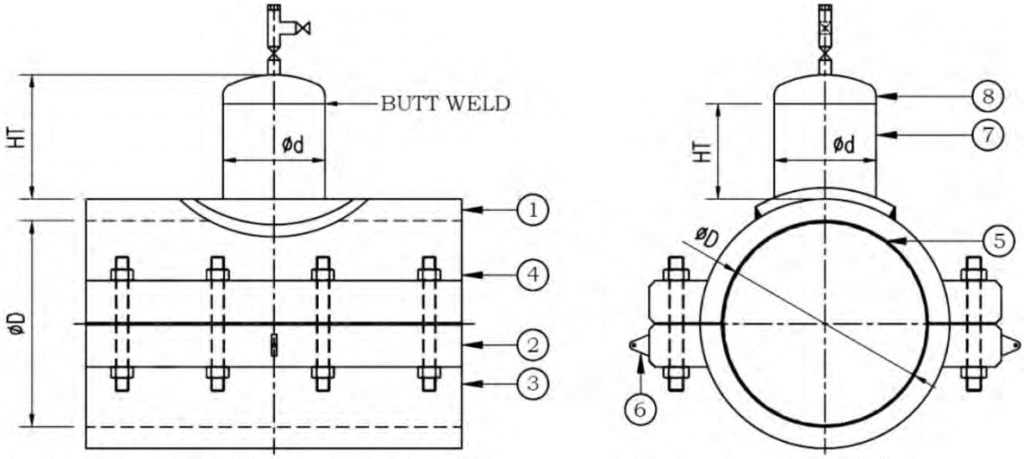
We are World Wide Service Provider.
We Manufacturer, Fabricator, supplier and exporter of Encapsulating Type Leak Clamp in MIDDLE EAST: Saudi Arabia, Iran, Iraq, Uae, Qatar, Bahrain, Oman, Kuwait, Yemen, Syria, Jordan, Cyprus, AFRICA: Morocco, Nigeria, Algeria, Angola, South Africa, Libya, Egypt, Sudan, Equatorial Guinea, The Republic Of Congo, Gabon, Tunisia, Uganda, Ghana, Senegal, Liberia, NORTH AMERICA: USA, Canada, Mexico, Panama, Costa Rica, Puerto Rica, Trinidad and Tobago, Jamaica, Bahamas, Denmark, EUROPE: Russia, Norway, Germany, France, Italy, Uk, Spain, Ukraine, Netherland, Belgium, Greece, Portugal, Hungary, Albania, Austria, Switzerland, Slovakia, Finland, Ireland, Croatia, Slovenia, Malta, Bulgaria, Turkey, Montenegro, Romania, Azerbaijan, Czech Republic, ASIA: India, Singapore, Malaysia, Indonesia, Thailand, Vietnam, South Korea, Japan, Sri Lanka, Maldives, Bangladesh, Mayanmar, Taiwan, Cambodia, SOUTH AMERICA: Argentina, Bolivia, Brazil, Chile, Venezuela, Colombia, Ecuador, Guyana, Paraguay, Uruguay, Peru