We are manufacturer, Exporter and Supplier of Vent Plug Type Leak Clamp are an essential part of our suite of pipeline integrity products. Available in a wide variety of sizes, ratings and arrangements, the clamp product line can be supplied independently or as an add-on to larger repair systems.
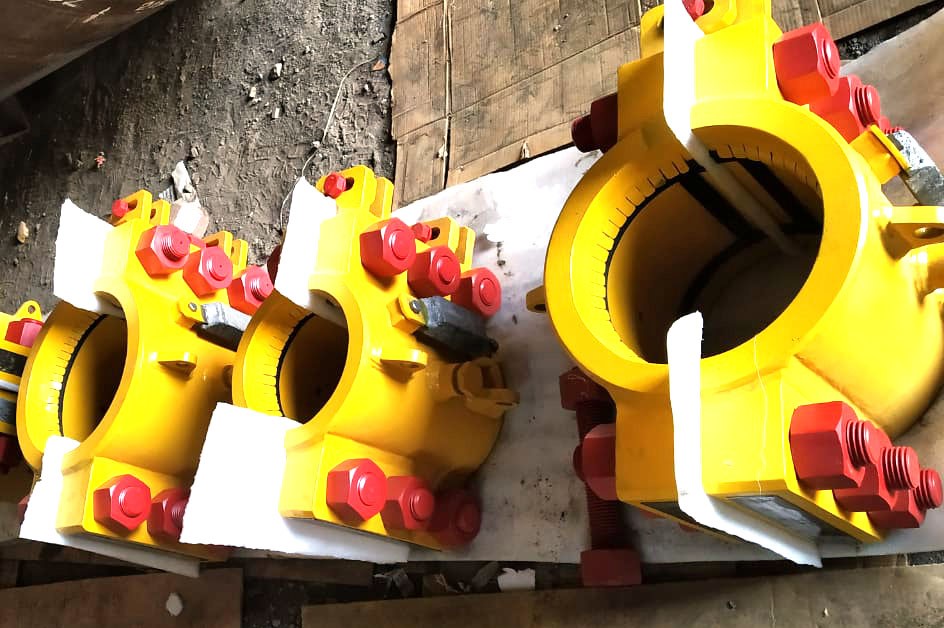
What is Vent Plug Type Leak Clamp ?
The sealing arrangement provides full containment around the damaged section of pipe (leak sealing only). If required, we can design the clamp to have a gripping section to provide a fully permanent structural repair that can be DNV-GL Product Certified.
Suitable for onshore, topside, diver installed or deepwater remote repair, our engineered MORGRIP clamps provide an increased lev-el of safety and reassurance when repairing critical pipelines or being stored as part of an emergency pipeline repair system or contingency plan.
Our clamps are application specific and designed, forged and fabricated to the exact requirements of the operator and repair location. This bespoke service ensures a fully configurable solution of the highest quality.
Indicative Drawings

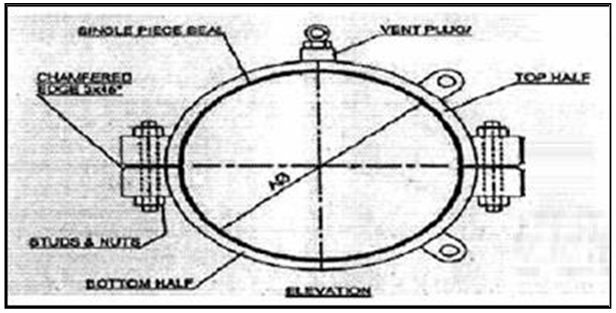
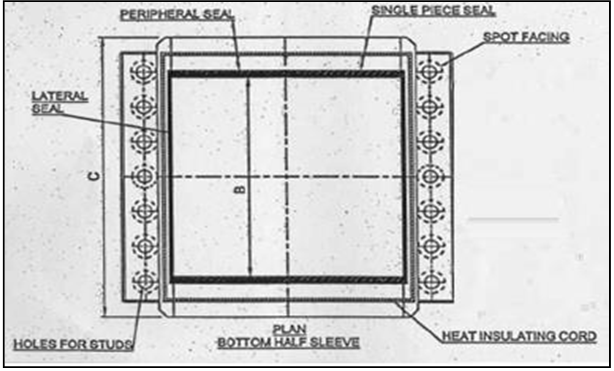
Special Specification For Vent Plug Type Leak Clamp:
1) The Clamp consists of Two Halves with one half having a vent plug. The same needs to be considered during design.
2) The Clamp shall be provided with all associated parts for successful and convenient
installation at site . Vent plug, Pressure G auge and lifting belts are to be provided as a
minimum.
3) The vent plug shall be used to fix vent pipe for venting of gas outside of pit to a farther point.
4) The Clamp shall be suitable for welding to mainline at a convenient time after installation.
5) One Spare set of seal shall be provided in Nitrogen Purged Aluminium casing.
General Technical Specification
Split sleeve type leak clamp assembled with vent plug, studs, nuts and best quality seating material
whole body as per the specification for R-LNG/ NG pipelines as mentioned below: –
Sl. No. | Description | Parameters |
1 | Design | As per API6H/ ASME SEC VIII DIV.1 / ASME SEC VIII DIV.2 , ASME-B 31.8, OISD 226 |
2 | Service/ Product to be handled | Re-Liquefied Natural Gas (R-LNG)/ Natural gas (NG) |
3 | Size/Class | Suitable for fixing on Spiral / Longitudinal weld pipe of grade |
4 |
Body | i. Carbon steel plates of weld-able quality (Carbon equivalent maximum – 0.25%), ii. Shell – API 5L Grade (Seamless /SAW) of equivalent of pipe grade / higher grade or ASTM A 516. iii. Stiffener – ASTM A105. iv. Longitudinal length of leak clamp should be minimum |
5 |
Studs | i. Alloy steel weld able conforming to ASTM A193- B7 / EN- 19 (minimum 7 nos. studs on either side). Preferable size stud (Diameter) should be 7/8”. ii. Studs length 4 nos. (Two on each side) should be 12- inch length and balance 9-inch length. iii. All stud / bolts supplied shall be painted with anti- rust varnish for preservation. |
6 |
Nuts | i. Alloy steel weld able quality confirming to ii. ASTM A194 Gr. 2H/ EN- 8 iii. Spot facing of the nut seal shall be carried out and no washer shall be used for tightening the nuts. iv. All nuts supplied shall be painted with anti-rust varnish for preservation. |
7 |
Sealing Material | i. There shall be sealing ring groove of appropriate size on the inner side of the leak clamp body on periphery of clamp. The molded, best quality “Buna N” rubber, shall cover the groove and covered surface between groove. ii. The mi nimum thickness of rubber packing material shall be6mm. iii. Suitable Welding Heat Insulation Cord to be provided iv. Shelf life of complete material should be minimum 4 year (confirmation is required from bidder in writing) v. The Seal Material of Clamp shall be suitable for hydrocarbon with following specifications: – Material: bunan Shore hardness: 80 +/- 5 A Tensile strength: 150 kg/cm2 minimum Elongation at break: 150% minimum. Compression set: 15% max. |
8 |
Edge Preparation | i. Edge as per ASME B -31.8 shall be done to be welded including nuts & studs of leak clamp. ii. The circumferential ends shall be chamfered (approx 45 deg.) down to thickness of the pipe as per ASME B 31.8. |
9 |
Hydro test Pressure | 29.0 kg/cm2 for Class 150 at ambient temperature. 152.0 kg/cm2 for Class 600 at ambient Temperature. The seals shall be replaced upon completion of hydro test. Testing shall be carried out in presence of Owner’s representative. No visual bulge shall be accepted during hydro test. |
10 |
Inner surface painting (uncovered by seal) | Two coats of Zinc Silicate primer with minimum Coating thickness of 100 micron uniformly applied on body (uncovered by seal) of the leak clamp. |
11 |
Outer surface painting | Clamps to be painted with airless spray gun. Primer: Zinc Silicate – 75DFT, Intermediate Coat – MIO 50DFT, T op Coat – Epoxy Polyurethane – 40DFT |
Specific Information:
Sl. No. | Description | Remarks |
1. | The fittings shall be inspected at vendor’s works and raw material at the pipe/plate supplier’s mill/outside laboratory of repute. | 1. Chemical composition and Mechanical properties shall be checked for base metal as per relevant material standards and this specification, for each heat of steel/materials a drawing of sample & testing shall be witnessed by TPI (Third party Inspection) and/or Owner. 2. Chemical composition and Mechanical properties shall be checked for fasteners and sea ling material (BUNA-N) as per relevant material standards and this specification. 3. If required, chemical composition and mechanical properties may be veri fied/rechecked at third party lab and shall be witnessed by owner and/or TPI. All incidental costs shall be borne by supplier. 4. Tensile, yield, elongation, chemical composition & Hardness value to meet the material specification. 5. Plates used for fittings shall be ultrasonically examined for lamination in accordance with ISO12094. Acceptance level B1 for the body, and E1 for the longitudinal edges. Vendor shall arrange test arrangements. 6. When fittings of size >18″ NB are manufactured, the fitting of each diameter and wall thickness shall be ultrasonically checked for sufficient wall thickness in areas where minimum wall thickness is expected. |
2 | Physical Dimensional Check | 1. Visual inspection-100% Witness by TPI (Third party inspection) and/or Owner. 2. Physical Dimensional Check shall be witnessed 100 % by TPI (Third party inspection) and/or Owner. |
3 | Ultrasonic testing of weld ends for lamination/cracks /other defects up- to a length of 50 mm & Other testing | 1. Ultrasonic Testing–Random Witness by TPI (Third p arty inspection) and/or Owner. All weld ends shall be 100 % ultrasonically tested for laminations and crack up-to a length of 50 mm. Lamination/Cracks/other defects shall not be acceptable. Weld repair on bevel end is not permitted. |
|
| 2. D.P. Test: 100% Dye Penetration test, |
|
| 3. Hydro Pressure Test: 100% hydro pressure as per API 6H. Documentary evidence for hydro-test pressure to be submitted. |
|
| 4. Stage wise quality assurance plan shall be carried out, consisting but not limited to: a. 100% MPI for stiffer to shell welds & hinge welds (fillet). b. 100% UT of vent plug welds(fillet). c. All shell plate shall be tested at -29 deg C. The impact strength acceptance 22J Individual and Average of 3 shall be greater than 27 J. d. The yield strength of Plate shall be greater than the yield strength of pipe. This is to ensure the fillet weld between Pipe and Clamp is of optimum thickness. |
|
| Stress Relieving check: Complete assembly shall be stress relieved after stiffener welding and before machining. Test reports on Stress relieving curves shall be reviewed by the owner or owner appointed TPI at party’s lab / testing |
4 | Final documentation check | Review |
Compliance To Specification:
The bidder should comply with the specification in totality and in token of confirmation the bidder shall return a copy of specification duly signed & endorsed.
Any remark by the bidder in respect of specification shall be mentioned herein below with proper reference to the clause and appropriate reason for the same.
Any remark directly or indirectly on the specification by the bidder made elsewhere in the offer shall not be considered by the owner.
BILL OF MATERIAL
Sr. No. | DESCRIPTION | MATERIAL | REMARKS |
01 | SPLIT BODY SHELL | ASTM A 516 GR 70/ API 5L GRADE (SEAMLESS /SAW) OF EQUIVALENT OF PIPE GRADE OR HIGHER GRADE OF RESPECTIVE PIPE GRADE |
|
02 | STIFFNERS | ASTM A 105 |
|
03 | STUDS | ASTM A193 GR B7 |
|
04 | NUTS | ASTM A 194 GR 2H |
|
05 | SEALING GASKET | BUNA ‘N’ |
|
06 | LIFTING HOOK | ASTM A 516 -70 |
|
07 | VENT PLUG ½” NPT 3000# | ASTM A 350 LF2 |
|
09 | HEAT INSULATING CORD – 8X8MM WITH MIN 2MM INSIDE THE GROOVE | TEFLON (PTFE) |
|
Note: Following requirements to be fulfilled by the parties:
Approval for QAP and manufacturing procedure, drawing of leak clamp, design of each clamp, Material test certificates before start of production / manufacturing.
We are World Wide Service Provider.
We Manufacturer, Fabricator, supplier and exporter of Vent Plug Type Leak Clamp in MIDDLE EAST: Saudi Arabia, Iran, Iraq, Uae, Qatar, Bahrain, Oman, Kuwait, Yemen, Syria, Jordan, Cyprus, AFRICA: Morocco, Nigeria, Algeria, Angola, South Africa, Libya, Egypt, Sudan, Equatorial Guinea, The Republic Of Congo, Gabon, Tunisia, Uganda, Ghana, Senegal, Liberia, NORTH AMERICA: USA, Canada, Mexico, Panama, Costa Rica, Puerto Rica, Trinidad and Tobago, Jamaica, Bahamas, Denmark, EUROPE: Russia, Norway, Germany, France, Italy, Uk, Spain, Ukraine, Netherland, Belgium, Greece, Portugal, Hungary, Albania, Austria, Switzerland, Slovakia, Finland, Ireland, Croatia, Slovenia, Malta, Bulgaria, Turkey, Montenegro, Romania, Azerbaijan, Czech Republic, ASIA: India, Singapore, Malaysia, Indonesia, Thailand, Vietnam, South Korea, Japan, Sri Lanka, Maldives, Bangladesh, Mayanmar, Taiwan, Cambodia, SOUTH AMERICA: Argentina, Bolivia, Brazil, Chile, Venezuela, Colombia, Ecuador, Guyana, Paraguay, Uruguay, Peru